3.3
Процесс изготовления заготовки для
оптоволокна
3.3.1
Химическое
осаждение из газовой фазы
Впервые
о методе химического осаждения из
газовой фазы (Chemical
vapor deposition
- CVD) было сообщено научно-исследовательскими
лабораториями Corning Glass Works
и Bell Telephone
(MCVD - modified chemical vapor deposition
- модифицированный метод химического
осаждения из газовой фазы).
В
этом методе добавляемая примесь SiO2
отложена слоями — начинающаяся со слоя
стекла для оболочки оптического
стекловолокна и оканчивающаяся слоем ядра
волокна - на внутренней стороне
вращающийся трубки (рис.3.4) которая нагрета
до 1600О C внешней горелкой.
Поскольку
каждый дискретный слой отложен друг на
друга, то при нагревании они одновременно
спекаются, чтобы сформироваться в
твердое стекло. Это происходит под
действием горелки, путем перемещения ее по
трубе в направлении выброса газа, оплавляя
слои кварца, отложенные перед горелкой.
Представьте
себе подобие токарного станка, в котором
на место резца установлена кислородно-водородная
горелка. В станок зажимается стеклянная
трубка и через нее на первом этапе
пропускается хлорид кремния и кислород (на
самом деле состав смеси более сложен). В
горячей зоне напротив горелки
синтезируется оксид кремния. Образуются,
фигурально выражаясь, пушинки окиси,
которые дрейфуют из горячей области в
более холодную и прилипают к стенке. Этот
процесс называется термофорезом, он
прекрасно описывается и объясняется
кинетической теорией.
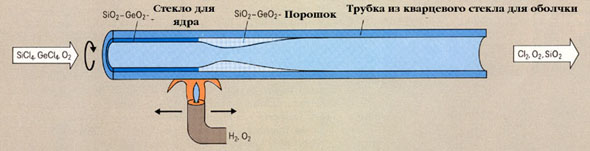
Рисунок 3.4
Процесс изготовления заготовки для
оптоволокна методом осаждения из газовой
фазы
Важно,
что осаждение происходит не в месте
нагрева пламенем, а перед ним - там, куда
пламя еще не дошло. На поверхности трубки
образуется пористый слой окиси, и,
двигаясь дальше, горелка его проплавляет -
остекловывает. Так получается слой
чистого стекла.
При
следующих проходах через трубку
пропускают еще и германий в виде хлорида.
Таким образом, легируют материал
световода, создавая в нем градиент
коэффициента преломления. После того, как
необходимое число слоев осаждено, подачу
хлоридов выключают, а температуру пламени
увеличивают - в результате трубка
плавится и схлопывается просто под
действием сил поверхностного натяжения.
Результатом
этого процесса будет твердое тело,
внутреннюю часть которого составляет
чистый материал для формирования ядра
оптоволокна, а внешняя часть из
материала покрытия оптоволокна.
Образцы,
подготовленные этим методом, могут
быть применены к различным типам
оптоволокна в соответствии с
отобранной толщиной, коэффициентом
преломления и других характеристик.
Размеры
заготовок, полученных этим способом,
позволяют изготавливать оптоволокно
длиной до 10 км. |
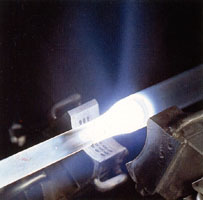 |
Рисунок 3.5
Процесс остекловывания в методе
осаждения из газовой |
Достижимые
величины затухания 1 дБ/км при длине волны l=1300нм могут в настоящее
время быть снижены до 0.5 дБ/км в
высококачественных волокнах. Причиной
этому, кроме свойственных преимуществ
осаждения из газовой фазы, является то, что
во внутренней части трубы, контакт
синтезируемого стекла с пыльным или
влажным воздухом полностью отсутствует.
В
основном этот метод разрабатывался
компанией AT&T, которая производит больше трети всего
объема волокна в мире. Этот метод
считается самым простым, и, кстати, в
отечестве только он реально и работал.
Однако для него нужна очень хорошая труба-заготовка
без включений, так как включения -
это центры напряжений, из которых может
начать расти трещина. С этим довольно
успешно борются путем химической или
огневой полировки поверхности трубок.
Преимущества
метода:
·
На всем протяжении процесса
изготовления каждого слоя сохраняется
закрытое пространство, что позволяет
избежать примеси посторонних материалов.
То есть, относительно легко могут быть
изготовлены волокна с малой величиной
затухания.
·
Легко управлять показателем
преломления слоя.
·
Может быть широко использовано в
изготовлении одномодовых волоконных
световодов.
·
Оборудование, использованное для
производства, относительно несложно по
конструкции и просто в управлении.
Неудобства метода:
·
Размер стержня заготовки ограничен
размером установки и трубкой кварцевого
стекла. Поэтому, стержень не может быть
сделан очень большим или длинным и
соответственно волокно не может быть
сделано очень длинным, в среднем от 3 до 5 км,
с максимумом от 20 до 40 км.
·
Должна использоваться только
заготовка из кварцевого стекла. Трудно
предотвратить диффузию ОH ионов и H2
из трубки заготовки к ядру волокна.
·
Возможно снижение показателя
преломления в центре ядра.
·
Так как горение и остекловывание –
происходит за счет наружного обогрева
трубки пламенем горелки,
производительность наплавки не такая
высокая, как ожидается от расхода
нагревающего горючего газа. Скорость
напыления - приблизительно от 0.5 до 2 г / мин.
Благодаря простоте
оборудования и его управления этот метод
широко используется во многих странах.
Окисление кремния и хлористых
германиев может также быть инициировано
плазмой. Метод названный позже PCVD (Plasma
chemical
vapor
deposition)
– метод осаждения из газовой фазы
полученной путем плазменного распыления.
Данный метод впервые был разработан
фирмой Philips.
Поскольку
зона образования газа может быстро
перемещаться по трубке, в короткий отрезок
времени возможно нанести сравнительно
большое количество тонких слоев,
производя в результате однородные профили
без видимых границ перехода от слоя к слою.
3.3.2
OVD-метод
(outside vapor deposition)
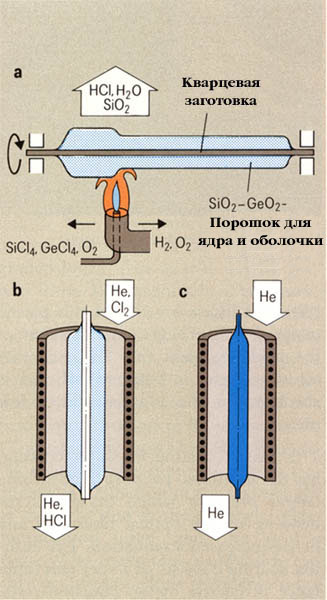 |
Другой
метод, которым пользуется фирма Corning,
называют еще внешним осаждением (в
отличие от первого - внутреннего) -
стекло осаждается на огнеупорный
стержень прямо из пламени горелки, куда
подаются хлориды исходных веществ.
Поскольку
осаждение происходит в атмосфере
пламени, в таком материале остается
много воды, получившейся в результате
окисления водорода. Поэтому, после того
как центральный стержень вынимают,
приходится продувать заготовку хлором,
который экстрагирует воду. И только
после этого заготовка остекловывается.
Перечисленные
выше три фазы процесса, а именно -
осаждение на огнеупорный стержень,
сушка и остекловывание, происходят
последовательно. Поэтому каждая фаза
может быть оптимизирована отдельно,
что позволяет достичь высокой скорости
осаждения материала применяя этот
процесс.
Кроме
того, скорость осаждения увеличивается,
так как поверхность подкладки
увеличивается с каждым последующим
слоем, что является положительным
коэффициентом в увеличении
относительной скорости процесса. Высокая
производительность наплавки (4,3 г/мин)
соответствует производительности 5 км/ч. |
Рисунок 3.6
a)
Изготовление заготовки методом OVD
б) С последующей сушкой
в) и спеканием |
При
соответствующей оптимизации процесса сушки, этот метод также может
использоваться для того, чтобы производить волокна с малыми потерями,
сопоставимыми по качеству с полученными внутренним осаждением трубки.
Преимуществами
этого метода являются:
·
отсутствие предела размера стержня
заготовки; поэтому волокно может быть
сделано большой, непрерывной длины,
например, 50-100 км;
·
осаждение, дегидрация и процессы
спекания отделены друг от друга; Так как
гидролиз произведен прямым обогревом с
горючим газом, то материал осаждения
производится быстро, производительность
наплавки - приблизительно 5 г/мин или больше;
·
отсутствие необходимости в какой-либо
подложке в основание; возможность
изготовлять все искусственные волокна.
А
неудобствами то, что:
·
при использовании этого метода все
химические реакции происходят на открытой
площади, что способствует более легкому
доступу для примесей. Чтобы предотвращать
это, должно быть подготовлено чистое
пространство, которое охватывает все
пространство реакции или оборудования;
·
смещение исходного материала может
причинять структурные нарушения в центре
ядра;
·
во время снятия сырьевого материала с
заготовки на внутренней стенке трубки
происходит натяжение, которое приводит к
появлению трещин и иных нарушений в
структуре волокна. Такое иногда случается,
когда коэффициенты теплового расширения у
ядра и оболочки разные. Из за этого
получение волокон с высокой NA
затруднительно.
Решение этой проблемы было найдено в
последнее время. Например, относительно
растягивающего усилия, слой с NA = 0.3 может
быть сделан, понижая
в максимально возможной степени разность в
коэффициентах теплового расширения
материалов покрытия и ядра.
3.3.3
VAD-метод
(axial vapor deposition)
В
третьем методе, разработанном японскими
фирмами, среди которых NTT, "Sumitomo" и
др., реализована более сложная
конструкция. Заготовка растет из
затравки, расположенной на определенном
расстоянии выше пламени горелки,
имеющей сложную слоевую структуру, как у
рулета.
В
середину пламени подают смесь хлоридов
германия и кремния, затем слой буферного
газа, потом только хлорид кремния для
чистого стекла, потом опять буферный газ,
и, в конце концов, на краю горелки,
кислород с водородом - то, что,
собственно говоря, и горит.
Вещество
осаждается на только что созданную в
этом же процессе поверхность. Однако
расстояние до этой поверхности должно
быть строго фиксированным, и заготовка
постоянно отодвигается от пламени
горелки.
Таким
методом можно создавать заготовки,
которых хватает на несколько тысяч
километров волокна, а в принципе процесс
может быть непрерывен - по мере
изготовления заготовки из нее же можно
вытягивать волокно. На сегодняшний день
это единственный метод позволяющий
осуществить производство непрерывного
оптического волокна. |
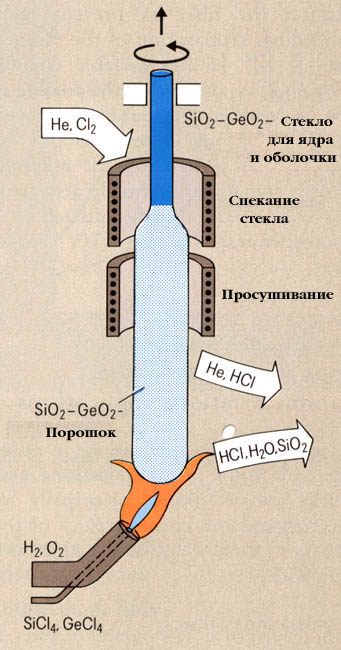 |
Рисунок 3.7
Изготовление заготовки VAD - методом |
Преимущества этого метода
заключается в том, что
·
заготовка для оптоволокна может быть сделана непрерывно бесконечной
длины;
·
пламя горелки не двигается, и коэффициент газов, текущих от нее -
всегда константа;
·
производительность наплавки - приблизительно от 1 до 3 г/мин, с максимумом
приблизительно 6 г/мин;
·
волокно с малыми потерями может быть легко изготовлено при
использовании процесса обезвоживания;
·
SM волокно легко изготовляется процессом VAD.
Неудобства заключаются в:
·
трудном управлении пламенем для того, чтобы сделать необходимый
профиль;
·
трудностях в изготовлении волокна с широкой полосой пропускания.
3.3.4
Сравнение методов получения
заготовки для оптоволокна
|
MCVD
|
PMCVD
|
PCVD
|
OVD
|
VAD
|
Химическая
реакция
|
окисление
|
окисление
|
окисление
|
гидролиз
|
гидролиз
|
Подача
тепла
|
кислородно-водородная
горелка
|
плазма
(1 атм.),
кислородно-водородная
горелка
|
микроплазма
(10 торр)
|
кислородно-водородная
горелка
|
кислородно-водородная
горелка
|
Скорость
осаждения, г/мин
|
|
3
- 6
|
0,5
– 2,5
|
5
|
3
- 6
|
Эффективность
осаждения, %
|
50
- 60
|
70
- 90
|
SiCl4
= 100
|
50
- 70
|
50
- 70
|
Размер
заготовки (волокон. км)
|
5
- 10
|
20
- 50
|
5
– 10
|
>50
|
50
- 100
|
Контроль
поверхности
|
очень
легко осуществим
|
легко
осуществим
|
очень
легко осуществим
|
легко
осуществим
|
Для
SM волокон легко осуществим, для GI
волокон требуются некоторые
технические приемы
|
Применение
|
AT&T
и многие страны
|
AT&T
(в разработке)
|
Philips
|
Corning
|
Япония
|
|